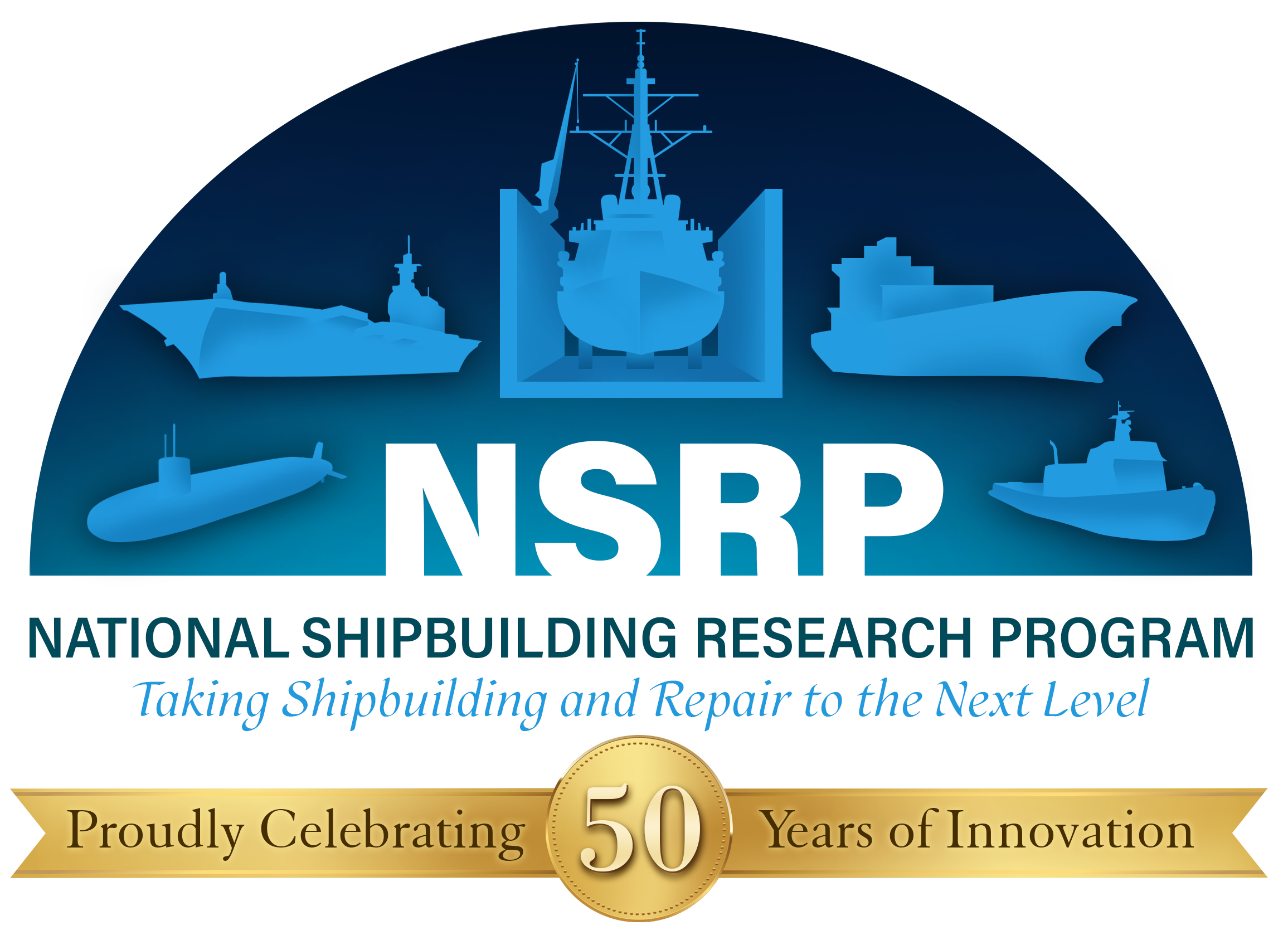
2021 NSRP All Panel Meeting Virtual Poster Session
National Shipbuilding Research Program
Filter displayed posters (64 keywords)
Tracks
▼ ManTech - Institute for Manufacturing and Sustainment Technologies (iMAST) Back to top
Institute for Manufacturing and Sustainment Technologies (iMAST)
Tim Bair, Tim Eden, Brenda Kephart
▼ NSRP - Business Technologies Panel Back to top
Structural Interface for Automated Compliance Checking
Steve Boisvert, Patrick David
LiftShip 2
Pat David
NSRP Advance Knowledge Provisioning Using Artificial Intelligence (AI) & Augmented Reality (AR)
Pacific Shipyards International | Conrad Shipyard, LLC | Fincantieri Marine Systems NA
▼ NSRP - Electrical Technologies Panel Back to top
Electrical Connector Standardization: Reduce connector variation to lower ship costs.
Larry Boyce | Rickey DeLoge | Paul Fellows | Mike Binekey | Tru Nguyen | Greg Stevens | Maurissa D’Angelo | Joe D’Angelo | John Walks | Harold Howard | Jason Farmer | Christopher Nemarich | Peter Andrich | Mark Smitherman |
Fiber Optic Distributed Temperature Sensing for Remote Monitoring of Electrical Systems
Linda Tomasi, Giovanni Tomasi
Advanced Topside Lighting - For TOC Reduction through Solid State Lighting Technologies
Giovanni Tomasi
Shipboard Fiber Optic Cables Design Enhancement
Billie Jo Mitchell, Giovanni Tomasi
The project met the objective to improve the resiliency and reduce Total Ownership Cost by identifying ways of making the fiber optic cables more robust and reducing the cost of installation. In addition, the project also identified an area where the cable cost can be reduced and the performance improved by re-evaluating the requirements for the outer jacket materials. The requirements driving the use of the higher cost thermoset jacketed cables (hot fluid immersions) may not be very important; better performance in areas considered more critical such as resistance to abrasion can be achieved by revising these requirements and allowing the use of more durable thermoplastic jacket materials.
Fusion Splice Enclosure at Equipment
John Mazurowski, Jason Farmer, Perry Haymon, Dan Morris, Shane Baker, Lucas Cashdollar, Harold Howard
▼ NSRP - Environmental, Health & Safety Panel Back to top
Identifying, evaluating, and mitigating ocular hazards in laser processing
Melissa Klingenberg, Stephen Brown, and James Brooks
Meeting ID: 161 724 6456 Passcode: 895448 One tap mobile +16692545252,,1617246456#,,,,*895448# US (San Jose) +16468287666,,1617246456#,,,,*895448# US (New York) Dial by your location +1 669 254 5252 US (San Jose) +1 646 828 7666 US (New York)
▼ NSRP - Research Announcement Projects Back to top
Tele-Welding: Leveraging Skilled Welders Through Remote-Access Operation
Connie Reichert LaMorte
The EWI-led joint research team of Newport News Shipbuilding, General Dynamics-Electric Boat, Robotic Technologies of Tennessee, and Visible Welding is currently completing a Navy-sponsored project through the National Shipbuilding Research Program (NSRP) to develop a mechanized welding system completely controlled by a worker who is remote from the welding site. The worker receives feedback from the operation and its environment via welding sensors, arc view cameras, and a real-time livestream of the entire process. The mechanized equipment can be operated through a control tool such as a computer mouse, haptic stylus device, or welding torch-like device attached to a desktop robot.
The first phase of this project centered on researching and developing technologies that, when combined, allow a worker to make a weld remote from the operation, but in 100% control of the welding process. A proof of concept was demonstrated in May 2020 where welding was completed at EWI by operators located in New England. The second phase of this project has centered on integrating down-selected technologies including a haptic stylus device and arc sensors onto both a mobile platform and a portable cobot arm. The final step of this project includes validating the technology with remote welding demonstrations on selected shipyard applications in May 2021.
Interface Design for Insulated Bus Pipe (IBP) to Navy Equipment
Dr. Patrick Lewis
▼ NSRP - Ship Design & Material Technologies Panel Back to top
Robotic Arc Directed Energy Deposition Additive Manufacturing for Shipbuilding
Dennis Harwig
The focus of this project is to develop robotic arc DED AM technology for shipbuilding. The objectives of this project are: • Develop digital data workflow (DDW) competencies for robotic arc DED AM of metals • Develop DED AM process models for arc processes, consumables, and shipbuilding material applications • Establish robotic computer-aided modeling (CAM) models for existing robot cells at EWI and shipyard partners • Develop process-feature-property relationships to establish structural properties, create build parameter windows, and build representative prototype process qualifications • Establish a standardized robotic arc DED AM gantry for large area/large volume AM to minimize system costs for wide scale implementation in shipbuilding and install a test bed version of the gantry at EWI for a range of applied research and prototyping services • Establish robotic arc DED AM training seminars and workshops for ongoing technical services to shipyards • Establish ongoing technical services for developing process-feature-property relationships, develop parametric CAM models for different arc welding process-consumable combinations, and build representative process qualifications to validate soundness and properties • Determine application opportunities and implementation priorities for robotic arc DED AM at American and Navy Shipyards
Minimum Standardized Content to Enable a NAVY Digital Enterprise
Ariel Bond
Simulation Workflow Development for Additive Manufacturing
David Najera & Elliot Haag
▼ NSRP - Ship Warfare Systems Integration Panel Back to top
TRITON: Dynamic Network Paradigm Analysis and Demonstration
John Mazurowski, Harold Howard, Sarry Habiby, Jason Farmer, Greg Stevens
▼ NSRP - Welding Technology Panel Back to top
Deep Penetration Laser-GMAW (HLAW) Welding
Jacob Hay, Stan Ream
▼ NSRP - Workforce Development Panel Back to top
Certificate Program: Shipbuilding Industry Marine Designer Training
Kyle Jellison, General Dynamics, Bath Iron Works
The curriculum itself is structured as a one-year apprenticeship program that can be registered in any state’s DOL. It includes approximately 144 hours of specific training for the shipbuilding designers, and is intended to coincide with a learner’s work experience once hired. Used as a one-year apprenticeship or just a 3-week training program, this training is designed for the attendee to earn a certificate distinguishing him or her as a knowledgeable and competent shipyard marine designer.
Certificate Program: Shipbuilding Industry Manufacturing Technician Training
J. Scott Christman, Ph.D.
The curriculum itself is structured as a one-year apprenticeship program that can be registered in any state’s DOL. It includes approximately 144 hours of specific training for the “desk plate”, and is designed to coincide with a learner’s work experience once hired. Used as a one-year apprenticeship or just a 3-week training program, it is intended for the attendee to earn a certificate distinguishing him or her as a knowledgeable and competent shipyard production craft mechanic.